- By: Admin
- July 2, 2024
- 2138 views
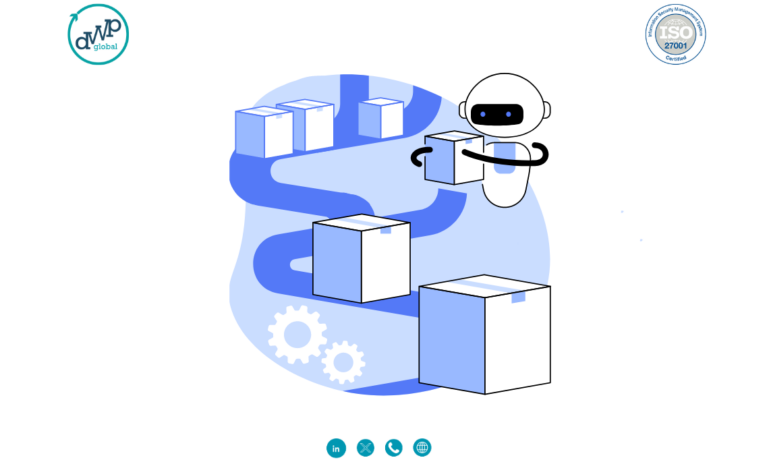
Optimizing Manufacturing Work Orders with Artificial Intelligence
Background:
Founded in 1880 and headquartered in Elk Grove Village, Illinois, our client specializes in providing fare collection solutions for public transit systems across North America. For over 40 years, they have been partnering with transit agencies to enhance ridership and revenue through innovative, equitable, and connected fare systems. Their solutions aim to simplify operations, improve the rider’s experience, and ensure secure transactions. They serve over 400 transit agencies, with a strong focus on customer care and support.
Problem Statement:
The client’s current quote to manufacturing process is cumbersome and time-consuming due to the need for extensive customizations for each customer order. The process involves verifying compatibility with existing systems and manually entering orders into SAP, leading to delays and inefficiencies.
Key Challenges:
- Complex Customizations: Every customer has distinctive needs for safeguarding their confidential data.
- Time-Consuming Compatibility Checks: Orders must be checked across various databases to ensure compatibility with existing systems.
- Manual Order Entry: Sales requests are manually entered into SAP, transforming them into manufacturing work orders, which is a labor-intensive process.
Proposed Solution:
The implementation of an AI-driven solution aims to streamline the quote to manufacturing process, reducing the time and effort required.
- AI-Powered Chat Bot/Web Application: Sales teams input customer orders into an AI-powered interface, initiating the workflow.
- AI-Based Recommendation System (ARS): The system queries databases for various combinations and flags any customer-specific customizations.
- Step-by-Step Workflow Completion: Sales representatives select from AI-suggested options to finalize the manufacturing work order.
- Integration with SAP: Once finalized, the AI system uses REST API to automatically post the manufacturing order to SAP.
Workflow:
- Sales Input: Sales team provides moderated inputs into the AI interface.
- Database Query: The AI model queries databases for compatible equipment and customization needs.
- Recommendation Generation: ARS identifies and flags relevant customer-specific information.
- Order Finalization: Sales representatives complete the workflow using AI-generated recommendations.
- Order Posting: The finalized work order is automatically posted to SAP.
Benefits
Time Efficiency: Reduced time from sales request to manufacturing work order creation.
Accuracy: Improved accuracy in compatibility checks and customization requirements.
Automation: Less manual intervention, leading to faster order processing and reduced human error.
Conclusion
By leveraging AI, the client could significantly streamline their sales request to the manufacturing input process. This would not only reduce the time it takes to quote but also ensure a more accurate and efficient creation of manufacturing work orders. This case study serves as a powerful example of how Artificial Intelligence can be used to optimize business processes in the manufacturing industry.